トレーサビリティ
生産過程のトレーサビリティを全公開
全製品のトレーサビリティーを専用サイトにて公開しております。
私たちの商品についたQRコードを読み取っていただくと、コットンの産地から出荷に至るまでの工程を閲覧できます。
企業の透明性や信頼性がより求められる時代において、社会に誠実であろうとする想いから始めた取り組みです。
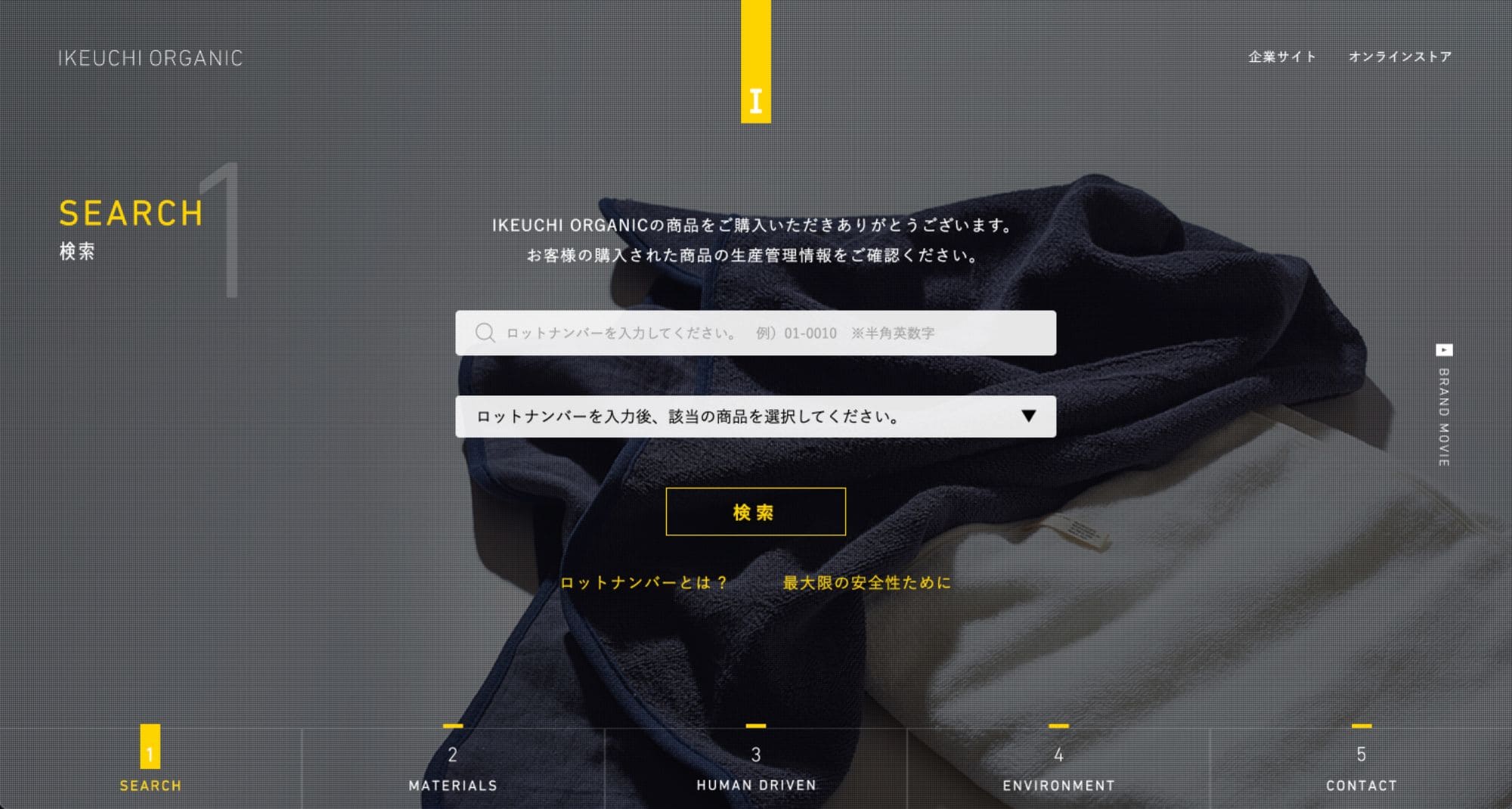
オーガニックタオルができるまで
一枚のタオルができるまで、綿花の栽培から始まり、綿花を紡績をして糸にし、糸からタオルを織り、染色するという多くの工程を経ています。
赤ちゃんが口に含んでも安全なオーガニックタオルをお客様にお届けするために、
IKEUCHI ORGANICではその工程の中に厳しい審査と品質基準を設けています。
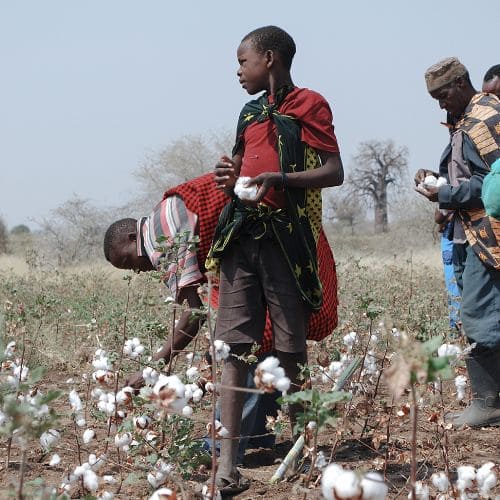
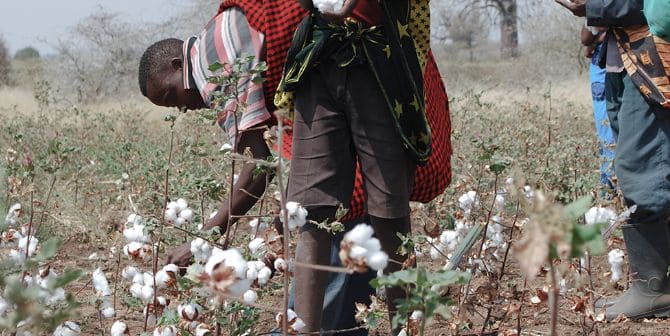
綿花栽培
有機農法で育てるコットン
IKEUCHI ORGANICのタオルの製造工程は、原材料のオーガニックコットンを育てることからはじまります。bioRe PROJECT(スイスREMEI社)の管理のもと、現地の農家たちは有機農法でコットンを栽培。春にまいた種は四方に枝葉を伸ばしながら60cmほどの背丈に成長し、夏にはレモン色の花を咲かせます。
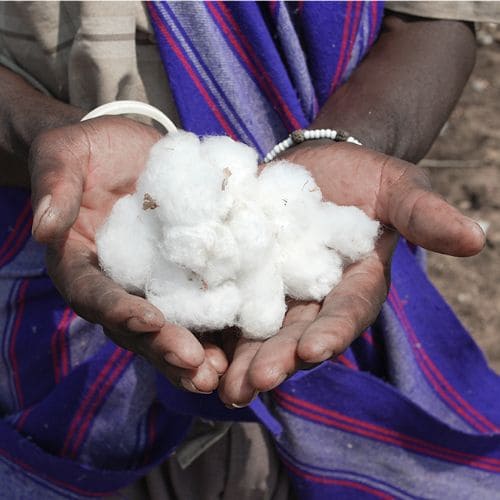
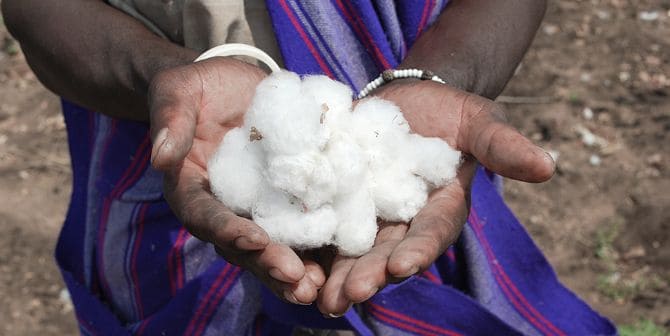
綿花収穫
ひとつひとつ丁寧に手摘みされます
コットンボールがはじけ、周囲の葉が自然と枯れたら収穫の合図です。枯葉剤は使いません。畑一面のあちこちでふっくらと開いたたくさんのコットンを、農家の家族も総出でひとつひとつ手摘み収穫していきます。
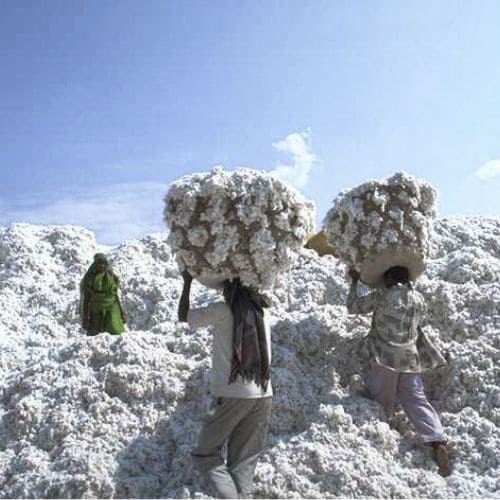
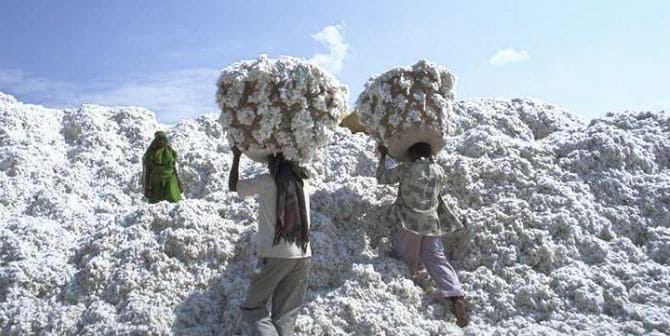
綿花集積
フェアトレードを生む
プレミアム価格
各農家が収穫したコットンは、集積場に集めて重量計測されます。このコットンを、bioRe PROJECTがオーガニックコットンの市場価格に15%のプレミアム価格をつけて買い取ります。このプレミアムは、過去5年のコットンの価格の平均値を元に、農家の代表者と決定した価格です。
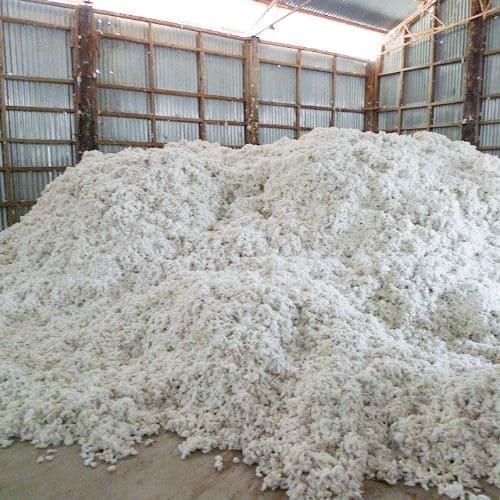
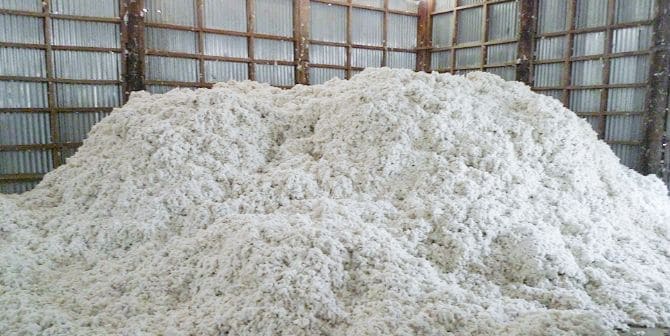
綿繰り(ジンニング)
余分な種を取り除きます
買い取られたコットンは、オーガニック認定の工場へ運びこまれます。ジンニング(綿繰り)工場でローラーにかけて繊維と種に分離していきます。ひとつのコットンボールには約15~30粒の種が入っており、重量に換算するとコットンボール全体の約2/3。90kgのコットンを収穫した場合、約60kgは種で、残りの約30kgがコットンの繊維になります。
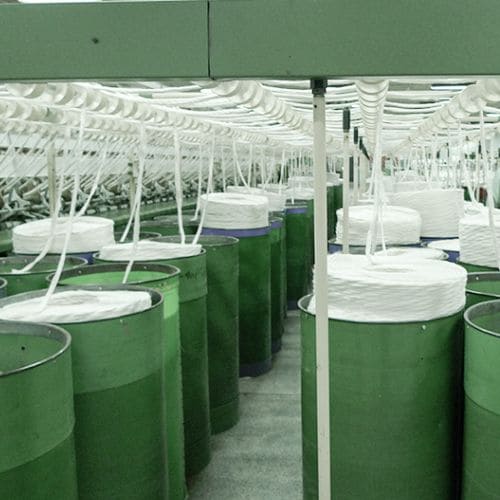
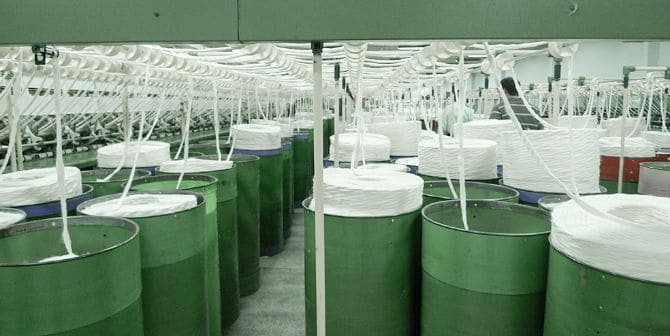
紡績
混打→練条→粗紡→精紡
農家がそれぞれの畑で栽培した微妙に風合いの異なるコットンを、均一な品質になるよう混ぜ合わせ(混打)、細かいゴミや短繊維を取り除いたら、一定の太さに引き伸ばしていきます(練条)。これに軽く撚りをかけながらさらに細く伸ばした後(粗紡)、精紡工程において、所定の撚りと太さの糸に加工されます。
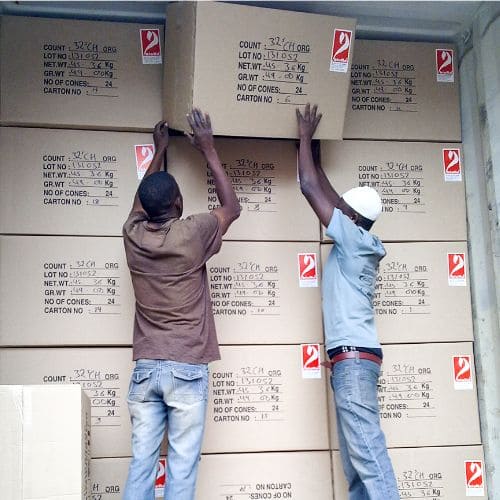
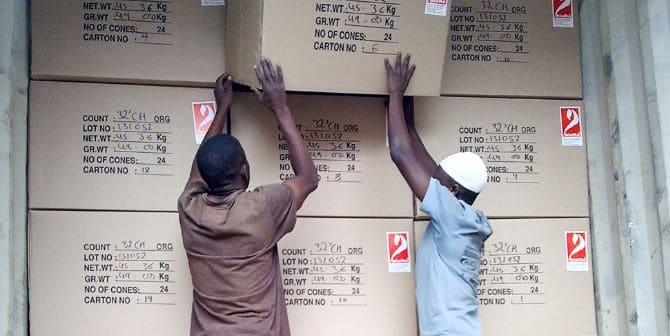
輸送
はるか彼方から
ゆっくりと船で運ばれます
コーンと呼ばれる管に巻かれた原糸はコンテナに詰められ、生産地であるタンザニアやインドの港を出港して日本へ輸送されます。輸送の途中でアジア各地(シンガポールや韓国)で積替えを経た原糸は、約4~6週間かけてIKEUCHI ORGANICのある今治の港へ着港します。
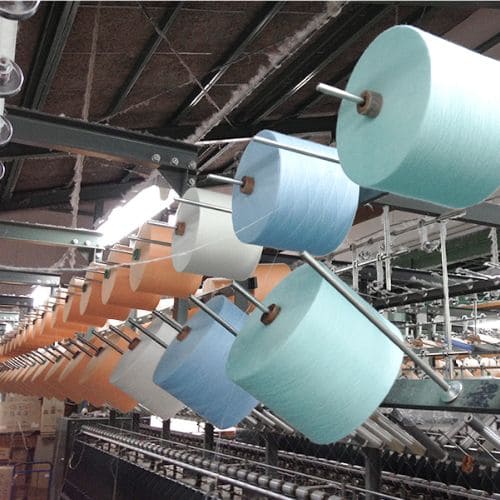
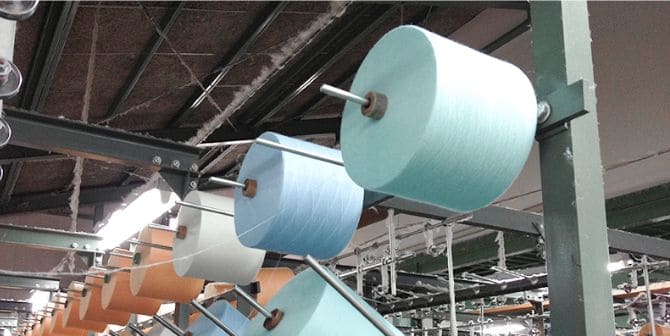
糸加工
タオルの風合いを
良くする為のひと工夫
日本に上陸した原糸は、素の状態です。例えば、この素の状態の単糸を2本の糸(双糸)に撚り合わせる場合に行うのが撚糸加工。コーンと呼ばれる円錐形の管に巻かれていた糸は、この工程を経た後で、加工がしやすいように円筒形のチーズ巻きに巻きかえられます。
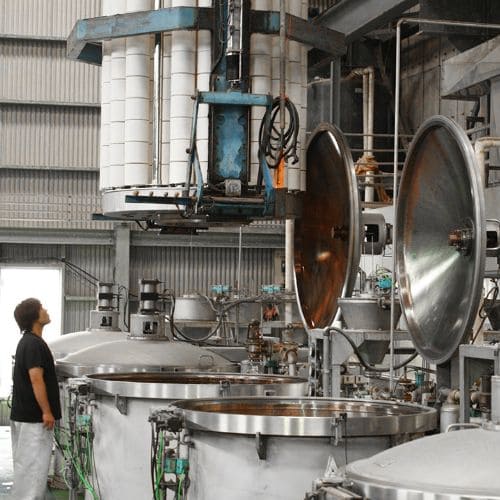
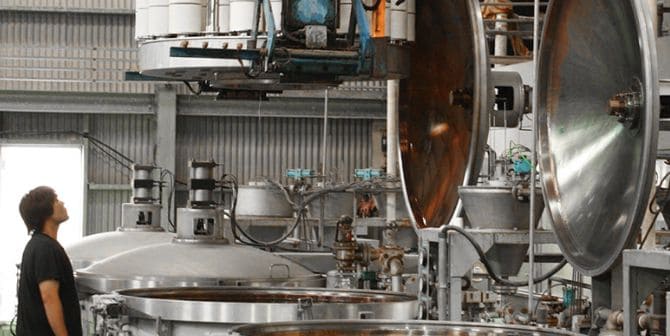
精錬・漂白・糊付け
実はコットンは
そのままでは水をはじくのです
コットンが本来持つ吸水性を高めるために、原糸に含まれる細かい不純物や油脂を取り除きます(精練漂白)。さらに、織機にかけて加工しやすいよう糊をつけます。IKEUCHI ORGANICでは、でんぷん糊を使用して環境負荷を減らしています。
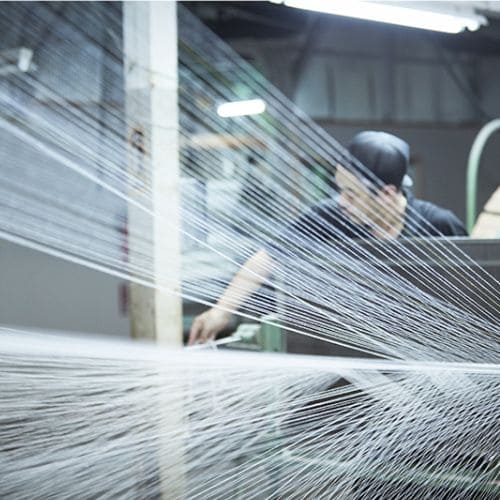
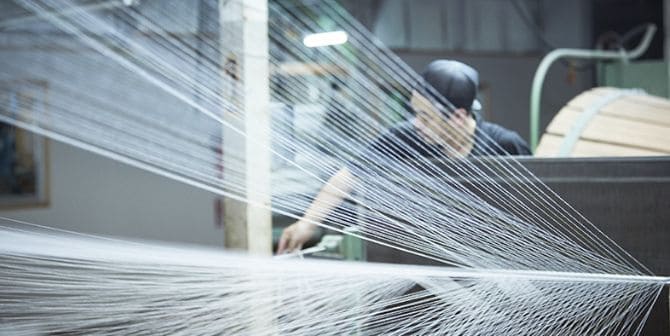
整経
ひとつひとつ丁寧に、
精密に並べます
加工を終え、木管に巻かれた糸がはじめてIKEUCHI ORGANICの本社工場に届きます。糸は約500本設置可能なクリールと呼ばれる機械にセットされ、織機にかけるための大きな「伸べ(ビーム)」という糸巻きに巻き取られます。一本一本設計図に基づいて並べられた糸に、適度なテンションをかけて巻き取ることで、様々な表情のタオルを織る基本となる伸べができあがります。
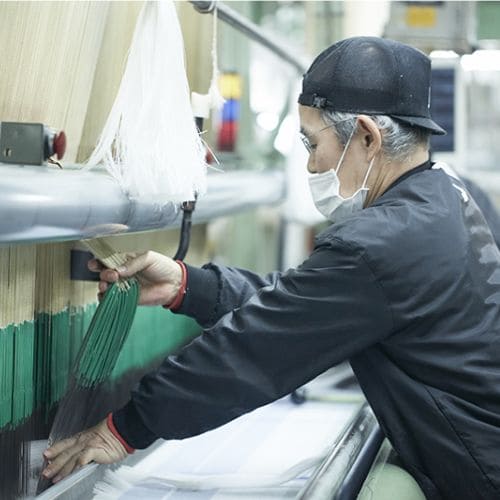
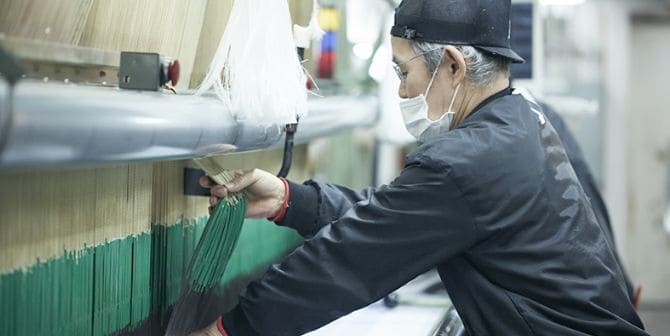
製織
職人の腕と技で、精密機械が動きだす
新しい伸べを織機にかけ、既に織機にかかっている糸とつなぎあわせます。約3000本~5000本にもなる糸を丁寧に櫛でとかし、手作業でタイイングマシンと呼ばれる機械にセットしてつなぎ合わせたら、いよいよタオルを織り始めます。かつての名織機、豊田自動織機の「TOYODA8」や最新の高速織機が並ぶ工場内では、熟練の技術の継承のために日々若手世代への研修も行われています。織りが終わった生地巻きは、織り傷や汚れがないか確認しながら空気を含むように解き放いた後、染色工場へ移動します。
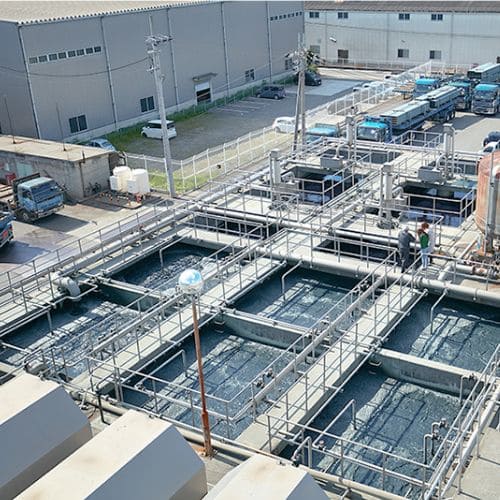

糊抜き・染色
世界最高水準の
排水浄化施設併設する染色工場
糸についた糊を洗い流した後は、真っ白な生地を染色していきます。染料には重金属を含まない反応染料を使用します。反応染料の使用での環境負荷は排水が最大の問題ですが、COD12ppm以下の排水浄化設備で瀬戸内海の厳格な基準をクリアしています。
西日本最高峰の石鎚山系地下水(ヴァージンウォーター)をたっぷり使って染色、洗浄を終えた生地は、乾燥機にかけられてパイルが立ったしっかりとした風合いに仕上げられます。
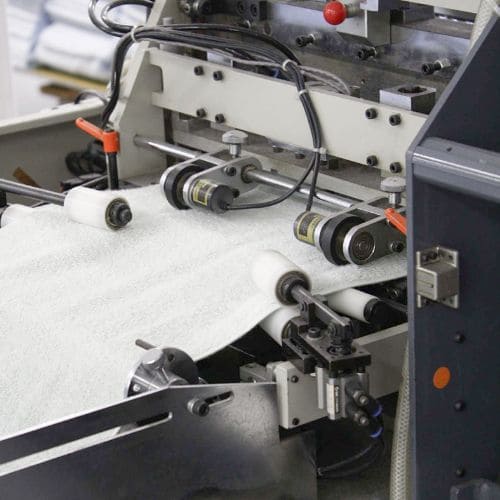
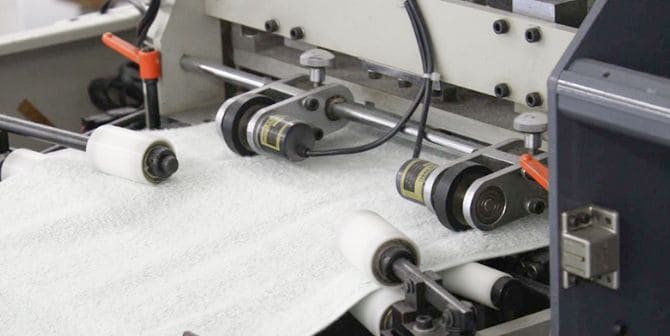
耳巻き・ヘム縫い
一枚一枚丁寧に、
人の手を通して作られます
スリッターと呼ばれる機械でタオル生地が1列ずつ裁断されていきます。そして、両端の耳と呼ばれる部分をミシンで縫ったあと、一枚一枚手作業でカットしていきます。上下の端はヘムと呼ばれ、ヘムを縫い終えるとタオルはやっと1枚の製品の形となります。IKEUCHI ORGANICの黄色いネームも、この工程で縫い付けられます。こうした熟練の技を通して一枚一枚のタオルに仕上がります。
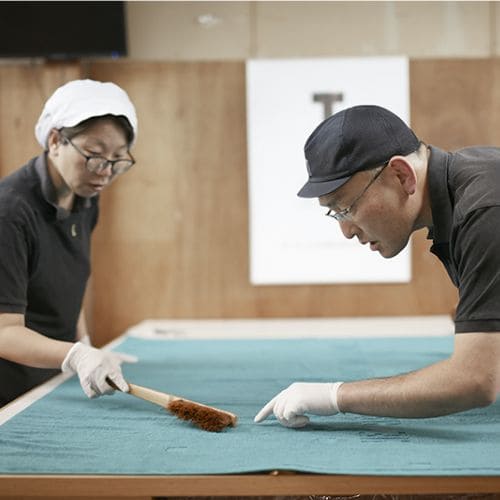
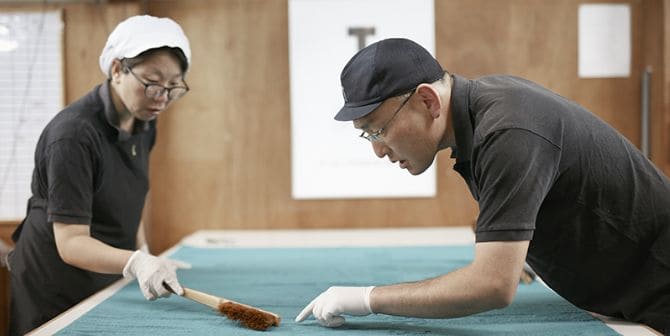
検品・出荷
最終の確認も人の目と手で行います
完成したタオルは、一枚一枚厳格な基準に沿って検品されます。織り傷がないか、パイル抜けがないか、汚れがついていないか、変形していないか。丁寧に検査して基準にクリアしたタオルだけが、IKEUCHI ORGANICのタオルとして工場から出荷されていきます。